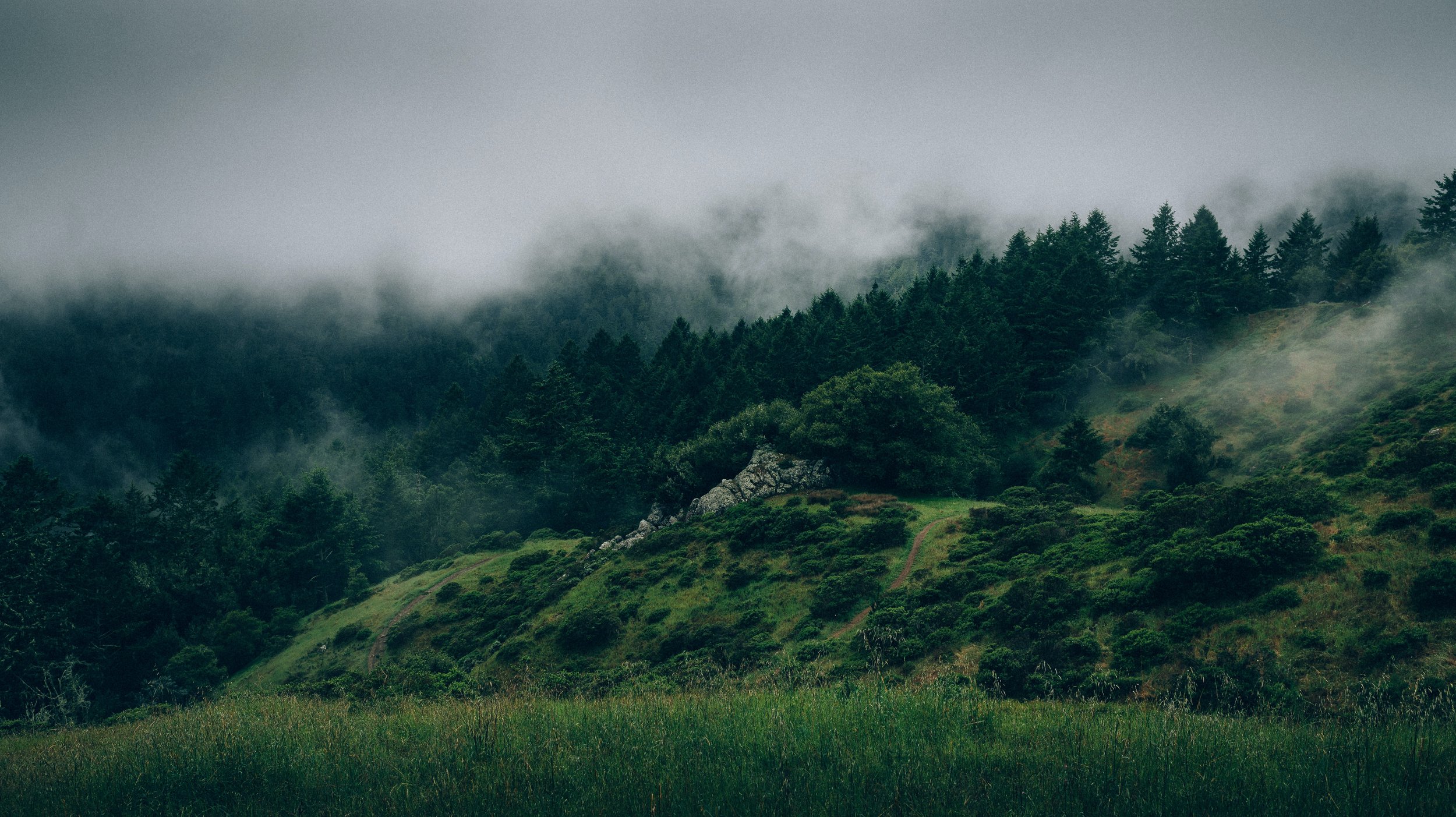
We turn waste textiles into value
Adding circularity to the textile industry through increased recycling
How recycled and worn-out fibers can be turned into something useful
The main idea behind the ShareTex process is to convert waste textiles into a cellulose pulp or a glucose solution, depending on the properties of the starting material. Cellulose can be valorized as such in those cases where the polymer is in good condition whereas complete depolymerization to target glucose production can be used in those cases where the polymer is degraded. Thanks to this versatile technology, ShareTex can valorize waste textiles that are not suitable for the production of new texile fibers, which adds an additional link in the waste hierarchy and minimizes the flow of waste textiles to incineration and/or landfills.
Background
The textile industry is today one of the largest industrial polluters and accounts for 3-4% of global carbon emissions
The global production of apparel and other textile fiber materials amounted to more than 120 million tons annually in 2019. A large amount of these textiles will currently end up as textile waste. Only 12% of all virgin textile fiber material is recycled at present.
To ensure a more circular economy and to reduce the environmental impact of the textile value chain we need to implement recycling of textile waste at a much greater scale. Furthermore, a large part of textile wastes, such as worn or repeatedly recycled cellulose-based fiber textiles, cannot be used to produce regenerated textile fibers in a sustainable or economical manner.
That’s why we started ShareTex.
What happens to the discarded textiles?
More than 80% of all produced textiles are eventually disposed of as waste, while only approximately 20% are separated and sorted for recycling or reusing purposes.
Approximately 70% of the textiles discarded as waste are landfilled, while the rest are incinerated. In the case of fabrics reclaimed for recycling/reusing, roughly half of them are recycled, 40% are sold as second-hand clothing and the remaining ends in waste streams.
There are many explanations for the low degree of recycling. One of the major difficulties for the recycling of textiles has been the need to sort waste textiles by fabric type. This is problematic as fiber blends are common in all sorts of textiles and efficient sorting and collection are still in its infancy.
An advantageous aspect of the ShareTex process is its ability to handle fiber blends (cellulosic, polyester, polyurethanes etc.). However, mechanical and/or chemical sorting upstream the ShareTex process is always preferred.
Process
The core of the ShareTex process is the conversion of cellulose-based waste textiles into cellulose pulp or a pure sugar solution
ShareTex targets the valorization of the cellulosic fractions in waste textiles regardless of their properties, imposing minimal or no requirements on the starting material. The fractions that cannot, technically or commercially, be effectively transformed into new textile fibers are instead transformed into a pure sugar solution of glucose. Sugar is a platform chemical that can be used for further conversion into numerous chemicals. Ultimately, these chemicals with a low carbon footprint can be used to improve the sustainability of various end-products, both within the textile sector and other industrial sectors.
The versatility of the process creates a cascading effect in which the value of the material can be recovered at the highest value possible depending on the properties of the cellulose polymer. Fractions with intact cellulose polymers are subjected to a dissolution/regeneration process to produce a cellulose pulp while fractions with degraded cellulose polymers are subjected to a pretreatment + hydrolysis process to produce a sugar solution. In this way, ShareTex can offer valorization alternatives for the entirety of this waste stream while mantaining the value of the material as high as possible.
Integration of waste textile processing in pulp mills
ShareTex is developing the possibilty to integrate the production of glucose from waste textiles within the operations of a pulp mill. The process would deliver high quality sugar solutions from cellulose-based waste textiles, while reducing the capital and operational costs in relation to existing recycling processes. The lower costs arise from the symbiotic relationship between the processes in terms of energy, material flows and know-how. The integration is based on using spent chemicals from the pulp mill operations as pretreatment agents to make waste textiles more amenable to depolymerization as well as using the excess heat available in the pulp mill to supply the energy required in the textile recycling process.
Product examples
Cellulose pulp
Cellulose pulp can be used as a starting material in the production of new textile fibers, which are called man-made cellulose fibers. Examples of this type of fibers are viscose and lyocell. However, cellulose pulp can also be used as a raw material outside the textile sector, for example in the production of cellulose derivatives or packaging materials.
Regenerated textile fibers
New textile fibers can be produced from wastes textiles either via cellulose pulp as an intermediate or directly respinning the fibers, depending on the quality of the waste. We have a versatile technology that ensures the material is valorized at the highest possible value, in order to maximize its circulation in the economy before it cannot be used anymore.
Glucose
Glucose is a sugar molecule that is widely used a starting material in the chemical industry. It is considered a platform chemical which means that a vast number of molecules can be obtained from it. For example, glucose can be used for the production of 1,4-butanediol, caprolactam, isobutene, etc. This molecules can be used to manufacture consumer products both within and outside the textile sector.
5-chloromethylfurfural
5-chloromethylfurfural (CMF) is a versatile raw material for many applications including the producion of p-xylene, a precursor in the production of polyester. CMF can also be used in the production of additives for aviation fuel as well as numerous commodity and speciality chemicals including furandicarboxylic acid (FDCA), surfactants, plasticizers and many more.
Who are we
Miguel Sanchis Sebastiá (CEO)
After studying chemical engineering in Spain, he did his PhD studies at Lund University at the Department of Chemical Engineering. His research on textile recycling laid the foundation for ShareTex. He has been leading the company from an early stage and is a recognized expert on sustainable fashion.
Mahla Bagheri (Lab engineer)
Mahla studied Natural Resources Engineering in Iran, during which she specialized in pulp and paper technology. She has advanced knowledge on wood and cellulose chemistry, which she combines with her practical experience in laboratory environments as well as in the pulp and paper industry.
Associated researchers
Ola Wallberg
Ola is professor at the department of Chemical Engineering at Lund University. Ola has a long experience in advanced fermentation process technology, chemical process design and process development.
Edvin Ruuth
Edvin is a PhD student at the Department of Chemical Engineering at Lund University. As the main part of his PhD studies, he is focusing on researching and developing new methods to recycle and valorize waste textiles.
News
04-06-2024
Ence and ShareTex sign MoU aiming to construct pilot plant
23-11-2023
Update after one year of RE:Spin project
04-05-2023
Did you say air filters from…discarded textiles?
04-06-2025
ShareTex receives Star Business Award for outstanding companies
Get in touch.
Interested in cooperating with us?